Technologies & Features
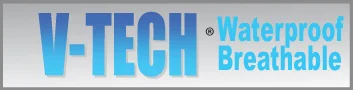
V-Tech®
V-Tech® is a complete protective membrane, designed with continuous microscopic pores, which allows heat vapor created on the inside to exit, while preventing water molecules from penetrating the garment.
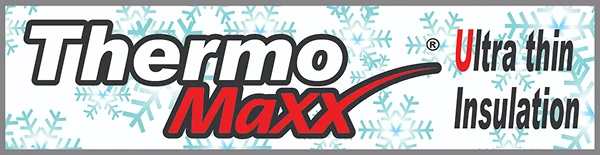
ThermoMaxx®
ThermoMaxx® is a high-tech, ultra-thin and light weight insulation that provides maximum warmth without the bulkiness.
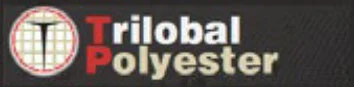
Trilobal Polyester
Trilobal Polyester utilizes triple twined polyester thread to create a cross section of fibres at regular intervals to form cells. These cells significantly increase the tensile strength of the garment over regular knit fabrics, effectively preventing tears from expanding to the next cell, while increasing the cut, tear and abrasion resistance of the garment.
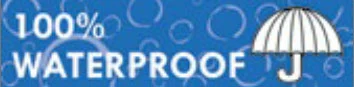
100% Waterproof
100% waterproof designation relates to the garment fabric’s permeability to water in more extreme conditions. This garment is either made of a material that water cannot penetrate, or has a coating of PVC that water cannot penetrate. This garment is designed for uses in prolonged foul weather exposure. Products with PU (polyurethane) coatings may claim to be waterproof, however to the porous nature of PU water can penetrate the fabric where hydro-static pressure exceeds 11psi. Hydro static pressure increases with wind and the amount of water hitting the fabric. Wind storms where rain is being forced down at +25KPH will likely penetrate a PU coated rain garment.
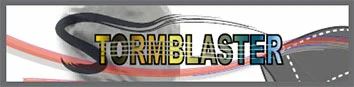
Stormblaster®
The Stormblaster® hood system reduces wind and rain exposure up the back of the jacket, while orienting the front close to the chin and cheek area. It has a safety “Tear Away” design, making it easy to remove and attach. Standard hoods are traditionally attached with hook-and-loop fasteners or buttons, leaving gaps that could allow water to travel up and around the neck area.
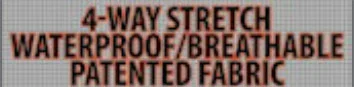
4-Way Stretch Waterproof/Breathable
Waterproof/breathable 4-way stretch patented fabric moves with your body, offering unparalleled flexibility while keeping you dry and cool at the same time.
Waterproof and Breathable
Waterproof
Viking® uses the most globally recognized Hydrostatic Water Pressure testing method – AATCC 127 to qualify our fabrics as being waterproof. The test material is subjected to steadily increasing water pressure on one face until water penetration occurs on the opposite face in three separate locations. The minimum standard for Viking® is 11.2 psi (pounds per square inch) or 784 mbar. This may generically be called 8,000 waterproof.
Breathable
Viking® uses the most globally recognized Water Vapour Transmission testing method – JIS L-1099 – Procedure B-1 to determine fabric breathability. This measures the ability of the fabrics to let steam or perspiration evaporate outside the textile. The test measures the amount of water in grams per sq. meter that migrates over a 24 hour period. Generally accepted ratings are listed in the adjacent table.
The minimum standard for claiming breathability in a Viking garment is 8,000 g/m²/24hours
5,000 – 8,000 g/m²/24hours = Good breathability
8,000 – 15,000 g/m²/24hours = Very good breathability
15,000+ g/m²/24hours = Excellent breathability
All waterproof Viking® recreational garments have seams that are double sewn, taped, and heat sealed.
Stitching and Seams
All Viking® garments are hemstitched and fully bar-tacked in all corners and stress areas. There are two common stitch types used in the outerwear market:
Hemstitching
Fabric is folded over at the edge and the layers are stitched together. This provides a clean hem edge, and eliminates fraying threads. Hemstitching requires more time and quality attention to produce.
Overcast stitching
This has a circular, continuous threading around the edge of the material. This system is much faster, and less expensive. The risk is that should this continuous thread break, the whole seam will unravel, also the fabric edge threads will “slip” pulling the trim stitching off the body of the fabric and commence unravelling
Double stitch vs. single stitch
Double stitching joints increases the tensile resistance of the seam, while reducing the specific pressure on each stitch. Should one stitch get snagged and torn, the garment will not unravel. Polymer film garments should be stitched at seams as well as heat sealed to ensure stress points do not tear or peel. All Viking® garments are double stitched for durability.
Bar-tacking
Bar-tacking is the reinforced repetitive stitching at critical tear points on a garment; these include pocket edges, arm and leg cuffs, button holes, and key stress areas in crotch, arm, and back.
You can rely on Viking® gear to keep you safe, dry, and warm on the coldest and rainiest of days, because every part of the Viking® garment has been meticulously thought out to deliver a comprehensive waterproof system that is also comfortable to wear. Each component and the stitching behind a Viking® garment give you the protection you need to Brave The Elements®.
Zippers
All Viking® garments use tooth zippers on front and boot closures. There are two common types of zippers used in outerwear:
Tooth Zippers
These are produced either in plastic or metal (brass). Tooth zippers offer the highest level of durability and longevity, and have the ability to withstand the torque of industrial and commercial uses. Highly recommended for front closures and boot zip regions.
Coil Zippers
These are considerably less expensive and are produced in plastic. Coil zippers are designed for low-pressure closures like pockets or arm vents. As front closures have a high risk of breaking or being damaged, tooth zippers are superior.
Embroidery Access Zippers
Whether you are an ad specialty or a promotional business, Viking® recreational garments are B2B friendly with our 14" embroidery access zippers.
High Visibility Standard: CSA Z96-22
Hi-Vis apparel is a function of two parts—retroreflective striping (most common is silver tape), and luminance of background material (generally fluorescent yellow-green or fluorescent orange-red).
Classes
Class 1
Apparel is a basic harness or stripes/bands over the shoulder and encircling the waist (stripes/bands only meet CSA/ANSI standard). Can be Level 1, 2, and FR retroreflection.
Class 2
Apparel is full coverage of upper torso—front, back, sides and over the shoulder (stripes/bands and background fabric both meet CSA/ANSI standard). Can be Level 1, 2, and FR retroreflection.
Class 3
Apparel is Class 2 apparel in addition to bands encircling both arms and legs (all stripes/bands and background fabric meet CSA/ANSI standard). Must have Level 2 retroreflection.
Levels
Level FR
This level allows for flame resistant garments with striping/bands where the total retroreflective level is at 20% of the level 2 requirement (FR treated fabrics lose lustre after treatment).
Level 1
Level 1 is a slightly lower performance level of the striping, but still requires the background material to meet CSA/ANSI Standards. Retroreflective level is at 70% of the Level 2 requirement.
Level 2
Level 2 is the highest level of retroreflection and requires the background fabric to meet CSA/ANSI standards as well as the striping/bands to meet the highest coefficient level (the brightest level).
High Visibility Standard: ANSI/ISEA 107-2020
This new standard combines the requirements of ANSI/ISEA 107-2010 and ANSI/ISEA 207, creating one standard that takes all occupational tasks into account.
Three Garment Types
The new garment types categorize hi-vis garments according to the different work environments of specific workers. When garment types are combined with the existing performance classes (1, 2, and 3), this new standard gives safety managers a larger variety of protection levels that considers more hazards.
Balance of Design & Logo Personalization
To maintain the balance in design, at least 40% of both the front and back of garments have retroreflective or combined-performance and background materials.
This new standard also permits company logos or any personalization to be part of a garment without compromising the total background area of the garment according to the following criteria:
- Personalization on background material should not exceed a total of 465 cm² or 72 in² on the front and/or back of the garment.
- Personalization on retroflective material should not exceed a total of 142 cm² or 22 in² on the front and/or back of the garment.
Flame-Resistant Performance Labeling
All Viking® and Open Road® ANSI/ISEA 107-2020 garments will be labelled to indicate flame resistance. Garments made from non-inherent flame resistant material or those not designed to meet FR standards will be differentiated on garment label by the following statement: “This garment is not flame resistant by ANSI/ISEA 107-2015 Section 10.5”.
Difference: Canada and USA Standards
Working Under The Sun
Hazard from the sun?
Sunlight, which is a major source of Ultraviolet (UV) radiation, has a wide range of positive health effects but, long-term sunlight exposure is known to be associated with the development of skin cancer, skin aging, immune suppression and eye diseases such as cataracts.
What are some health hazards of exposure to UV radiation?
Sunburn (Erythema)
Best-known acute effect of excessive UV radiation exposure. The severity of the effect depends on the wavelength, intensity, and duration of exposure.
Over the longer term, UV radiation induces degenerative changes in cells of the skin, fibrous tissue and blood vessels leading to premature skin aging, photo dermatoses and actinic keratoses. Another long-term effect is an inflammatory reaction of the eye. In the most serious cases, skin cancerand cataractscan occur.
UVB
UVB is a medium wavelength ultraviolet ray from the sun. UVB rays are the “burning” rays in the UV spectrum. UVB radiation ranges from 280 to 320 nanometers in wavelength. Some wavelengths in that range have greater potential to cause damage than other wavelengths. UVB radiation is stronger between late morning and early afternoon when the sun’s rays are directed straight down at the Earth.
All personnel working outside should be prepared to protect themselves from over exposure of ultraviolet radiation.
What about the ratings?
UPF
UPF stands for Ultraviolet Protection Factor. It is the ratio of the average effective ultraviolet radiation (UVR) irradiance transmitted and calculated through air to the average effective UVR irradiance transmitted and calculated through fabric. It is the amount of ultraviolet radiation that a fabric blocks. Fabrics are tested for UPF ratings.
The following fabric qualities contribute to the chances that a particular garment will have a good UPF rating:
– Darkness of color
– Tightness of weave
– Fiber Thickness – Heavier is better
– Resilience / stretch ability
So what does the rating mean?
The UPF ratings for the level of protection found in the fabrics are classified by ASTM International as follows: These ratings comply with AS/NZS 4399 Australian/New Zealand Standard for Sun Protective Clothing, tested under AATCC Test Method 183.
Most garments of a weight of 280gsm or higher should achieve UPF 50.
SPF
UVA
The UPF ratings for level of protection found in the fabrics are classified by ASTM International as follows: These ratings comply with AS/NZS 4399 Australian/New Zealand Standard for Sun Protective Clothing, tested under AATCC Test Method 183.
Most garments of a weight of 280gsm or higher should achieve UPF 50.
How to protect yourself?
What are some of the ways to protect yourself when working under the sun?
Ways to limit exposure to the sun’s UV radiation include wearing protective clothing and hats, and applying sunscreens.
Protective clothing can include long pants, hats, and long-sleeved shirts.
Viking UPF50+
This garments use specially treated pre-washed fabrics that blocks 97.5% of UV radiation in regular as well as lighter weight garments like t-shirts. The protection will not wash out with normal wear and care.
Sunscreens
Sunscreens are rated according to Sun Protection Factor (SPF), an index of protection against skin erythema (reddening of the skin). SPF ranges from 1-50 or more. The higher the SPF is, the more protection it offers from UVB radiation.
spf indication
SPF 15 sunscreen may absorb more than 92 percent of UVB radiation
SPF 30 sunscreen may absorb 96.7 percent
SPF 40 sunscreen may absorb 97.5 percent of UVB radiation
Standards vs Test methods:
Often users mix up the many standards and test methods related to FR garments. We will go through the most relevant standard performance specification, test methods, terms and give you a summary of what you should really be looking for when considering FR garments.
ASTM D6413
The USA Testing Method and requirement for determining a fabric’s resistance to ignition and ability to self-extinguish when exposed to an open flame.
CAN/CGSB 4.2 No. 27.10
The Canadian Testing Method and requirement for determining a fabric’s resistance to ignition and ability to self-extinguish when exposed to an open flame.
ISO 17493/ASTM F2894-12b
A testing method and requirement for determining a fabric’s ability to resist ignition, melting, or shrinkage in ambient temperatures at 260°C for 5 minutes.
ASTM F1930
A testing method using a manikin with a finished garment and using a heat flux of 2 cal/cm² over an exposure time of 3 seconds to determine the predicted second and third degree burn area. This test method duplicates a hydrocarbon flash fire incident, and predicts the garment’s protection against 2nd and 3rd degree burns.
Codes / Guides
NFPA 2112
This is the standard Performance Specification that will specify the minimum performance requirements and test methods for flame-resistant fabrics and components, and the design and certification requirements for garments for use in areas at risk of flash fires. Testing includes flame resistance (fabrics tested before and after 100 commercial wash/dry cycles), thermal protective performance (TPP), heat resistance, thermal shrinkage, and manikin flash fire.
NFPA 70E
Both of these code or guide are for electrical safety in the workplace, composed of procedures, policies, and guidelines.
What is HRC & TPP?
HRC is changing to Arc Rated Category (CAT)
HRC is an abbreviation for Hazard/Risk Category as determined by the ATPV (Arc Thermal Protective Values) or the amount of energy from an Electric Arc a fabric will resist. The change to Arc Rated Category is to remove the “risk”, and define the actual arc protection as “risk” to a worker is more a function of multiple factors that require a risk assessment or model. This standard does not address hydrocarbon flash fire peril. HRC is going to Arc rated Category as defined as follows:
TPP
Thermal Protective Performance of a fabric tested with radiant and convective energy to determine the total energy required to simulate a 2nd degree burn injury. The minimum requirement for a fabric used in a CGSB 155.20 garment is 6.0.
TPP in relation to CGSB155.20.2000
It is not enough that a fabric may have a TPP value of 6.0+; in order to meet the standard of CGSB 155.20, and provide the required amount of hydrocarbon flash protection to a user, the WHOLE garment must comply with the CGSB 155.20 standard.
Be careful about claims of “Fabric meets CGSB 155.20, or has a TPP value of 6.0+”.
To sum it up…
CAT/HRC is only used for electric arc, so a high CAT/HRC rating does not automatically imply that it will offer any hydrocarbon flash fire protection.
Depending on the material used, a high CAT/HRC garment may provide some inherent TPP value but unless stated, do not assume TPP rating.
Hydrocarbon Flash and Electric Arc
The correct standards for Hydrocarbon Flash Fire and Electric Arc protective clothing are:
- NFPA 70E, NFPA 2112-2012, CGSB 155.20-2000
- CGSB 155.22-2014, and ASTM F1506
Each of these standards has stringent requirements for compliance, lot
traceability, and independent testing. Manufacturers making any claims of
compliance to these standards should be able to provide extensive testing
reports in original state and after 50 washing cycles.
Limitations
Under each of the above standards, there is a requirement that each garment has a clear label that outlines the limitations, and use of the
garment for applications. All Viking® garments with claims of “basic” FR will be labelled as follows:
Attention
This garment has been tested in accordance with the test method CAN/CGSB-4.2 No.27.10 & ASTM D6413 Flame Resistance, Self Extinguishing for Momentary Contact with Open Flame.
In contact with flame, this garment will resist ignition, and / or self-extinguish. The intended use of the garment is for protection from liquids including water, oil, light acids and caustics. This garment also provides wind resistance and acts as a thermal layer against harsh elements, while providing increased visibility of the wearer. This garment is not intended as protection from hydrocarbon flash fires, electric arc hazards, or welding sparks.
What Sets Viking® Boots Apart from Other Brands?
We focus on safety—not as a guide—but as a philosophy, making sure every boot we produce exceeds the standards and embraces comfort and wellness for the wearer.
We have developed unique last designs that allow us to produce boots that fit like a shoe, our “Snug Fit”. We work with miners, foresters and firemen to understand their comfort issues, and introduced technologies in air and moisture control to help improve the wellness of those using our boots, and ergonomic insoles to enhance the comfort of the fit.
Snug Fit
Traditional “gum” boots, and injection molded boots are produced on a straight, widening shaft last, so as to make them strippable from the last. The result is a loose fit with little ankle and arch support, causing increased fatigue and an overall sloppy feel. Viking® developed new, innovative, multi piece lasts, allowing us to taper the ankle area of the shaft to create a form fitting and supportive boot that can be easily removed from the last. We developed a new insole system with an ergonomic design to support the arch and improve the stability of the fit—the resulting “Snug Fit” design boots. Slip-on boots that feel like they are laced on; superior ankle/heel support to reduce incidences of ankle roll-over; superior arch support to reduce fatigue, finally a gum boot that moves with you, as part of you. Now available in all Viking® light Chainsaw boots (VW58-1, VW59-1), Viking® Mining Boots (VW42), Viking® Ultimate Construction Boots (VW88), Viking® Firewall FR® Boots (VFW 60-1), Viking® Non-Safety Boots (VW22, VW23, VW29), Viking Handyman® Boots (VW3, VW 3-1) and Viking Firefighter® Boots (VW90, VW91).
Air, Moisture Control (AMC)
Viking® developed two socks to increase the wellness of the user of rubber boots.
VF22
The first is a dual layer thermal, acrylic/cotton, construction sockette that provides ventilation while wicking perspiration away from your feet. An external cotton layer to absorb and evaporate moisture. Acrylic fleece inside layer insulates while drawing perspiration from your feet to the cotton exterior.
VF25
The second was in response to abrasion and chaffing on the calve, due to perspiration buildup within the boot in more temperate environments (underground mining); we developed a triple layer Neoprene sock/bootie that transfers perspiration away from the calve, and through the top of the boot significantly reducing chaffing and abrasion.
Material
Rubber
Injection molded or handmade, rubber boots offer the highest level of abrasion, tear, and puncture resistance. Injected rubber boots can only offer limited safety features, being a steel toe cap and plate, with Electric Shock Resistance, whereas a handmade rubber boot can incorporate shin and metatarsal protection, chainsaw and circular saw protection, thermal heat and Hydro Carbon Flash fire protection, and one of the highest level of chemical resistance—safety features that provide workers with the highest level of safety assurance. With slip resistance the hot topic in safety today, rubber offers the highest level of slip resistance.
Injection Molded or Hand Made Industrial Safety Rubber Boots?
100% Waterproof Safety boots can be produced in two methods, by injection molding PU, PVC or TPR into a molded former, or by hand lasting layers of rubber. Injection molding is considerably more economical, but lacks the diversity in safety features a handmade boot can achieve. Handmade boots can use blended rubbers to achieve unique chemical, and abrasion resistances. Handmade boots can include metatarsal protection, as well as chainsaw and fire protection that injection boots cannot.
We focus on safety—not as a guide —but as a philosophy, making sure every boot we produce exceeds the standards and embraces comfort and wellness for the wearer.